DragX nano-scale molecular structures fill in and coat microscopic nooks and crannies in a pipeline’s Inner Diameter (ID) surface in a way that was not previously possible with conventional coatings. This function significantly increases the surface contact area, resulting in unsurpassed adhesion and creating a virtually impenetrable passivating barrier of corrosion and abrasion protection.
After application, DragX rapidly cures to reduce the pipeline’s surface roughness significantly. In field deployments, DragX has shown a reduction in pressure drop within a treated line by up to 25% when applied to a relatively clean, lightly corroded pipeline.
For comparison, traditional mechanical pigging and cleaning can only achieve an improvement of 10% in pressure drop – and this effect is only temporary. On heavily corroded lines, DragX has been demonstrated to reduce the pressure drop losses by a factor of 2.
Pressure Drop vs. Flow Rate
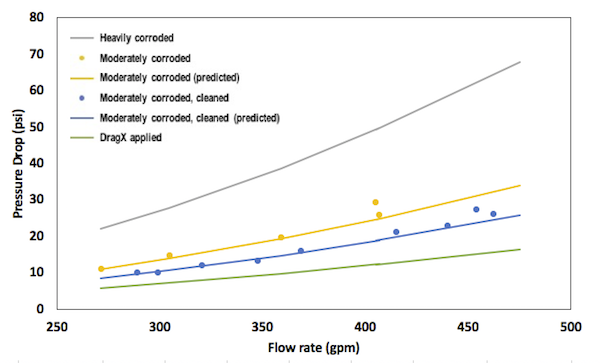
At an effective thickness of just 2mil, DragX reduces the surface roughness of treated pipes to as low as 60μin.
In field deployments, DragX demonstrated that, even on previously deteriorated or damaged surfaces, it could reduce surface roughness significantly. The result is an ultra-slick surface that reduces pressure drop vs. untreated pipe IDs by 20-25%.
DragX’s underlying nanocomposite technology creates an oleophobic, or water & oil-repellent, low-friction surface. By reducing the surface friction of the pipe ID, DragX reduces the need for costly inhibitors or continuous injection of costly flow assurance chemicals. In addition, throughput can be increased while pumping power consumption is reduced.
DragX has been shown to increase flow capacity at decreased pressures, even on de-rated pipelines. It is effective on all flow regimes and products (liquid, gas, multi-flow).
DragX Development
The underlying surface-modification nanotechnology developed for DragX was created with support from the U.S. Department of Energy (DOE), the U.S. National Energy Technology Laboratory (NETL), and the U.S. Environmental Protection Agency (EPA). DragX exhibits a pot-life of more than 70 hours, is effective at thicknesses of only 2mil, and cures in less than one hour. These attributes in the nanocomposite surface treatment make DragX an ideal solution for in-service pipelines, reducing costs and minimizing pipeline downtime.
DragX has undergone successful testing by Test America, Inc. with the support of the EPA for application to potable water lines and delivered successful, well-below contaminant results for EPA Method 524.2: Volatile Organic Compounds (VOCs), EPA Method 525.2: Semi-Volatile Organic Compounds (SVOCs), and EPA Method 200.8: Lead/Copper.
In conjunction with the RPSEA program with the NETL, tests at the Colorado School of Mines showed excellent asphaltene repellency and anti-hydrate plugging performance. Results on asphaltene repellency showed that DragX was 6x better than raw pipe and 5x better than an omniphobic alternative.
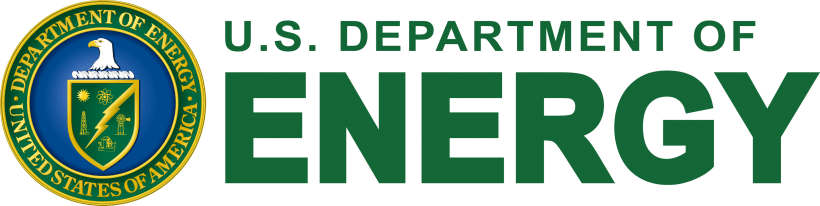
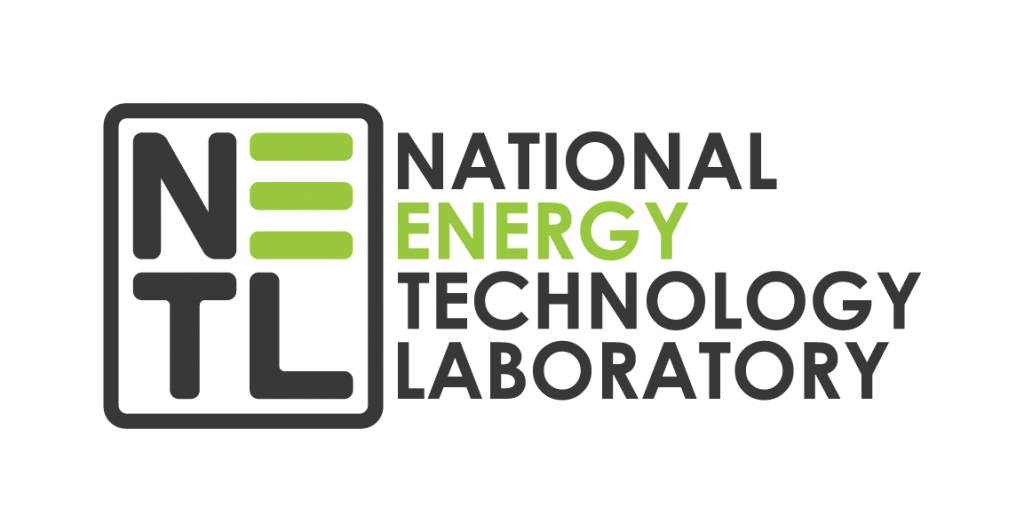
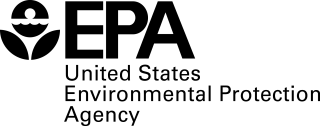
Omniphobic surface treatment videos
Hydrophilic & Hydrophobic Flow Behavior
Oceanit nanocomposite treatments were applied to sample pipes, demonstrating hydrophilic and hydrophobic flow behaviors. This video compares flow through an untreated pipe to both a 'water-loving' hydrophilic pipe and a 'water-repelling' hydrophobic pipe.
Omniphobic Wetting Behavior
Oceanit's omniphobic surface treatments create water- and oil-repellency on treated surfaces. These advanced nanocomposites create a low surface energy, hydrophobic, and oleophobic layer that imparts both chemical & corrosion resistance. In addition, the functionalized surface repels fouling.
Superhydrophobic Surface Behavior
Oceanit's superhydrophobic surface treatment creates an extreme water- and ice-repelling surface that prevents corrosion. The family of anti-ice coatings showed the lowest-ever adhesion strength rating by the Air Force Cold Regions Research and Engineering Laboratory (CRREL).
Contact Us
Would you like to learn more? Contact us to learn how DragX surface treatment can help you proactively manage risks, rehabilitate degrading lines, and keep your production flowing.